Custom made
Drohnen, die einen Blick von oben und die Sammlung von Daten aus der Luft ermöglichen, gibt es einige. Seien es Modelle „von der Stange“ oder auch individuell gefertigte Kleinserien. Um jedoch das Optimum aus den fliegenden Mitarbeitern herausholen und diese so effizient wie möglich nutzen zu können, müssen – je nach Betriebsszenario – zuweilen spezielle Modifikationen vorgenommen werden, um die Payload aufzunehmen. Immer häufiger hilft an dieser Stelle der 3D-Drucker.
Von Jan Schönberg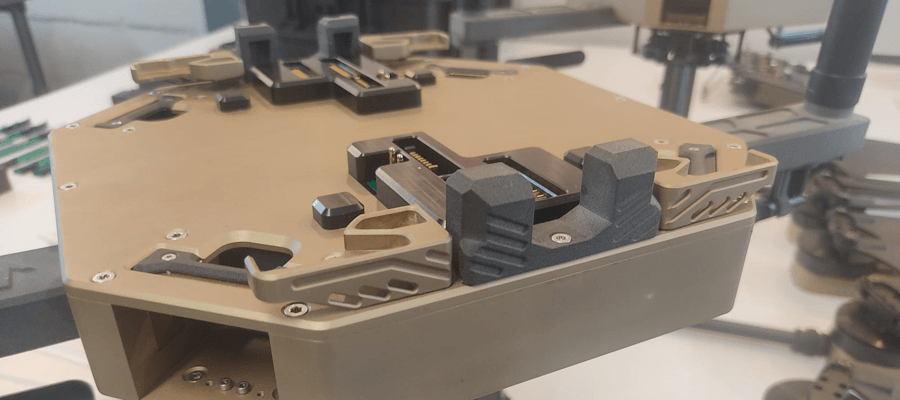
Naturkatastrophen, gesunkene Schiffe oder Verkehrsunfälle: In den Nachrichten sehen wir mittlerweile täglich Bilder, die mit Drohnenhilfe entstanden sind. Mit den Aufnahmen aus der Luft lässt sich ein besserer Gesamteindruck vermitteln. Doch UAS werden natürlich bei Weitem nicht nur für die Erhebung optischer Eindrücke genutzt. Sie versorgen Wissenschaftlerinnen und Wissenschaftler mit Daten, werden in der Landwirtschaft, dem Rettungswesen und zur Inspektion kritischer Infrastruktur genutzt. Die unbemannten Luftfahrzeuge lassen sich also sehr vielseitig einsetzen. Je nach Einsatzgebiet müssen die Drohnen unterschiedlichen Anforderungen gerecht und dementsprechend ausgestattet werden. So verändern sich die Art der Kamera oder die Befestigung der Nutzlast. Mit passgenau gefertigten 3D-Druck-Teilen lassen sich Drohnen einfach und kostengünstig an die verschiedensten Herausforderungen anpassen.
Erleichterter Prozess
Die Konzeption einer Drohne ist sehr komplex. Bereits die Positionierung einzelner Bestandteile bestimmt ihre Leistungsfähigkeit. Wenn beispielsweise GPS und Antenne in die richtige Position gebracht werden, bedeutet dies eine größere Reichweite und eine höhere Übertragungsqualität. Um ihre Aufgabe bestmöglich erfüllen, verlässlicher navigieren oder länger fliegen zu können, muss das unbemannte Luftfahrzeug samt aller möglichen Gadgets und Technologien auf die speziellen Anforderungen abgestimmt werden. Herkömmliche Fertigungsverfahren erschweren diese Anpassung. Die Herstellung von Bauteilen und die weiterführende maschinelle Bearbeitung mit Wasserstrahl- und Laserschneidverfahren ist teuer – insbesondere bei den erforderlichen komplexen geometrischen Formen.
So nutzt beispielsweise der Drohnenhersteller Nextech aus Südafrika einen 3D-Drucker des deutschen Unternehmens Formlabs, um die eigenen Produkte optimal auf spezifische Anforderungsprofile anpassen zu können. Konkret handelt es sich dabei um das Modell Fuse 1+ 30W, der nach dem Prinzip des Selective-Laser-Sintering (SLS) funktioniert. So können nicht nur individuelle Kundenwünsche erfüllt, sondern auch möglicherweise erforderliche Änderungen umgesetzt werden. Denn alles, was per CAD-Programm designt wurde, lässt sich vergleichsweise schnell und preiswert produzieren. Die digitalen Konstruktionsdaten der jeweiligen Drohne helfen bei der präzisen Druckplanung für die Zubehörteile. Beim SLS-3D-Druck schmilzt ein Laser ein pulverisiertes Kunststoffmaterial, beispielsweise Nylonpulver, exakt an den vordefinierten Punkten in der Druckkammer. So können komplexe Formen ohne zusätzliche Stützstrukturen gedruckt werden. Gleichzeitig wird ein ähnliches Gewicht wie bei den späteren Endverbrauchsteilen aus Kohlefaser erreicht.
Die individuelle Anpassung eigener Produkte an Kundenwünsche kann ein Wettbewerbsvorteil im Kampf um Marktanteile sein
Optimal angepasst
Mit dem additiven Druckverfahren werden Prototypen gedruckt, welche Funktionstests unterzogen und wenn nötig angepasst werden. Das ist praktisch, wenn sich beispielsweise das Gewicht oder die Umgebung der Drohne verändern. Jede Veränderung hat schließlich Auswirkung auf die Gesamtkonstruktion. In einem herkömmlichen Verfahren mit externen Dienstleistern wäre es für Nextech sehr teuer, Prototypen für einzelne Entwicklungsschritte herzustellen – die im Nachhinein vielleicht sogar nicht erforderlich sind. Die Entwicklung anhand von Prototypen ist jedoch wichtig, damit jede Drohne optimal auf ihr Einsatzgebiet angepasst ist. Mit dem additiven Verfahren kann das Team von Nextech komplexe Formen erstellen und verschiedene Versionen ausprobieren. Sollte sich die Anforderung ändern, kann mit geringem Aufwand ein neues Design gedruckt und getestet werden.
Verschiedene Arten von Kameras oder Sensoren, die an Drohnen befestigt sind, eignen sich für Unterstützung in der Landwirtschaft, dem Umweltschutz oder der Überwachung der Tierwelt. Die Kameras und Sensoren erfordern maßgeschneiderte Halterungen, um sie am Rahmen der Drohne zu befestigen. Jedoch ändern sich diese Halterungen bei jedem Projekt, sodass bei UAS mit Verbrennungsmotoren, die häufig für Langstreckenmissionen in unwegsamen Gelände zum Einsatz kommen, die Nutzlast manchmal weiter von der Treibstoffquelle entfernt oder in einem anderen Winkel angebracht werden muss. Die individuelle Positionierung ist wichtig, da sich die Treibstoffquelle auf langen Strecken erhitzen kann. Je länger die Strecke ist, desto größer muss der Abstand zwischen der Treibstoffquelle und den Kameras oder Sensoren sein. Damit die technische Ausstattung optimal funktioniert, darf sich diese nämlich nicht erhitzen.
Ein SLS-3D-Drucker und passende Materialien wie das Nylon-12-Powder von Formlabs ermöglichen es, schneller und kostengünstiger neue Flügelspitzen-Designs von Starrflüglerdrohnen zu testen als mit herkömmlichen Methoden
Eine Drohne für die Arktis
Ein besonderes Modell von Nextech ist die Atlas-T, eine Starrflüglerdrohne mit einer Spannweite von 3,2 Metern und einer Reichweite von 100 Kilometern. Diese wurde für ein Projekt mit der französischen Regierung eingesetzt. Dabei scannte und untersuchte ein Forschungsteam die schmelzenden Eiskappen in der Arktis. Die Atlas-T wurde dafür mit multispektralen Bildgebungsgeräten und speziellen Wärmebildsensoren ausgestattet. So konnten Erkenntnisse darüber gewonnen werden, wie der Ozean die Geschwindigkeit des Abschmelzens der Eiskappen beeinflusst. Um die empfindliche Technik zu tragen, hatte das Nextech-Team maßgeschneiderte Halterungen und Gehäuseteile für die Starrflüglerdrohne entworfen. Zudem wurden die Flügelspitzen individuell an die extremen Bedingungen angepasst.
Die Drohnenbranche ist sehr wettbewerbsintensiv und Unternehmen drängen sich um große Aufträge aus den Bereichen Regierung, Forschung und Landwirtschaft. Um an der Spitze zu bleiben, müssen Drohnenhersteller ihre Technologie ständig aktualisieren und anpassbare Optionen für jedes Projekt anbieten. Der Einsatz von 3D-Technologie ermöglicht es den Herstellern, in der Konstruktions- und Entwicklungsphase bestmöglich auf individuelle Anforderungen und Kundenwünsche eingehen zu können. Auf diese Weise lassen sich zudem Zeit und Kosten sparen, was als Wettbewerbsvorteil natürlich ebenfalls nützlich sein kann.